Air Tool Lubrication
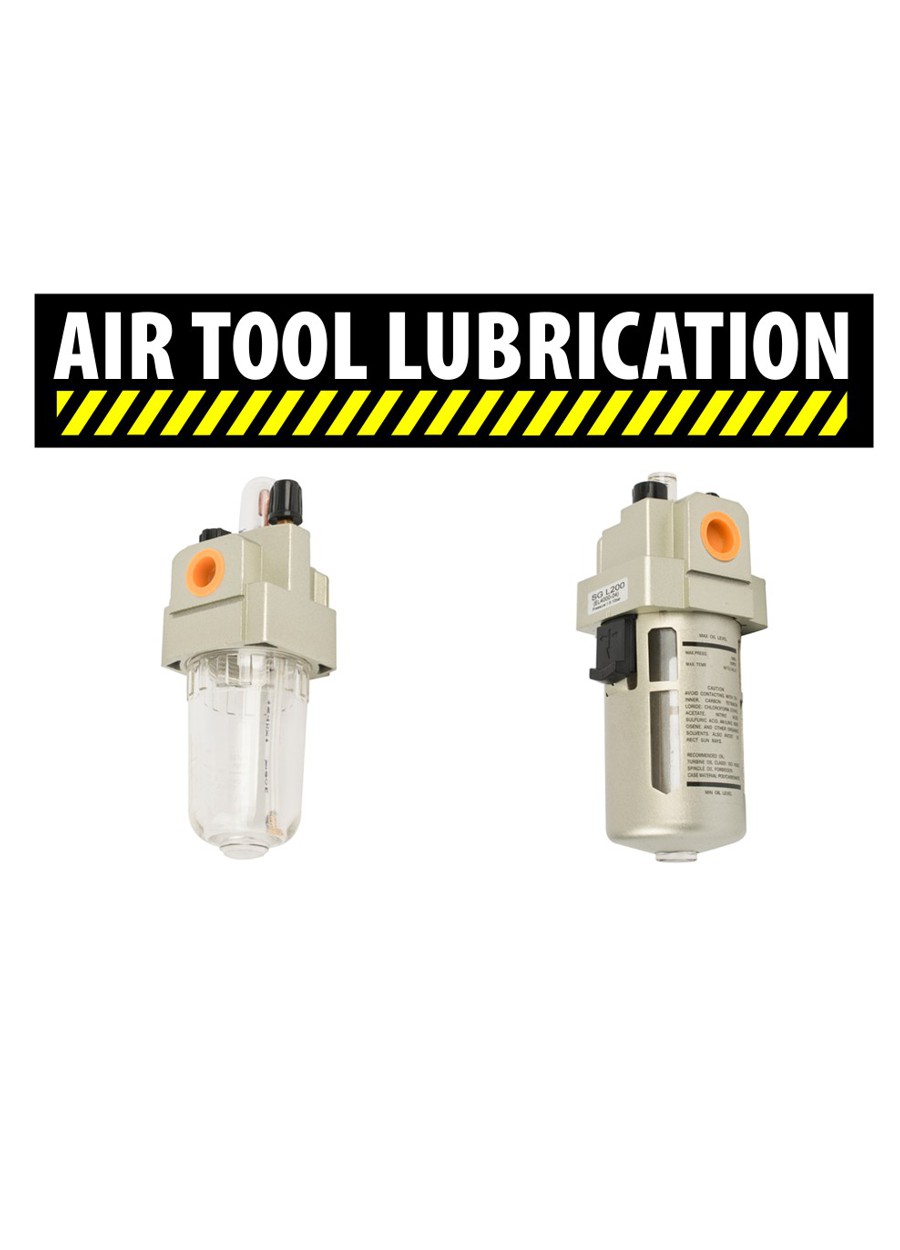
The in line lubricator:
Because of their design characteristics, all percussion air tools require some form of lubrication to reduce the friction and heat that can lead to premature wear of internal moving parts and/or possible failure of those parts. For construction and rental applications, the most common device used to provide lubrication is the in-line lubricator or oiler.
In-line oilers were designed to efficiently lubricate air tools and other pneumatic equipment downstream from the compressor. The oiler provides lubrication that allows moving parts such as pistons, tappets, and valves to operate freely with a minimum amount of friction. This reduced friction allows parts to perform to their design specifications eliminating the possibility of premature wear and failure that can occur from heat build-up. The flow of lubrication also acts as an internal cleansing system that deters natural dirt and contamination inside tools that are running in dusty environments from easily becoming stuck on internal surfaces and interfering with the performance of the tool. This natural cleansing effect of lubrication is important for all tools and can be further enhanced greatly by periodic flushing of the tool with some form of low flashpoint solvent.
The lubricator injects an aerosolized stream of oil into an air supply to provide lubrication to the internal working parts of pneumatic tools.
The compressed air enters the inlet port and passes over a needle valve orifice attached to a pick-up tube. This tube is equipped with a bronze filter, submerged into a reservoir bowl filled with pneumatic oil. Oil is pulled up by the venture effect and emitted as an aerosol at the outlet port.
The lubricator can be adjusted to release the correct amount of oil, depending on the amount of air flow. It should be the last element in the FRL (Filter- Regulator-Lubricator) unit. Only use pneumatic oil with the correct viscosity. SAE 10 or ISOVG 22 or equivalent lubrication. We have a pneumatic air tool oil available in our range of products AT OIL.
If an FRL is connected backwards with Lubricator fitted first, then the oil-laden compressed air will interfere with the air pressure in the regulator. The oil will also be separated from the air stream and then drained from the filter. The lubricator needs to be installed within 15 meters of the workstation.
Air hoses used in conjunction with lubricators can not be used for applications where contamination will affect results, for example, spray painting.
The best results are found when running at 6,3 bar (90psi) pressure measured at the tool.